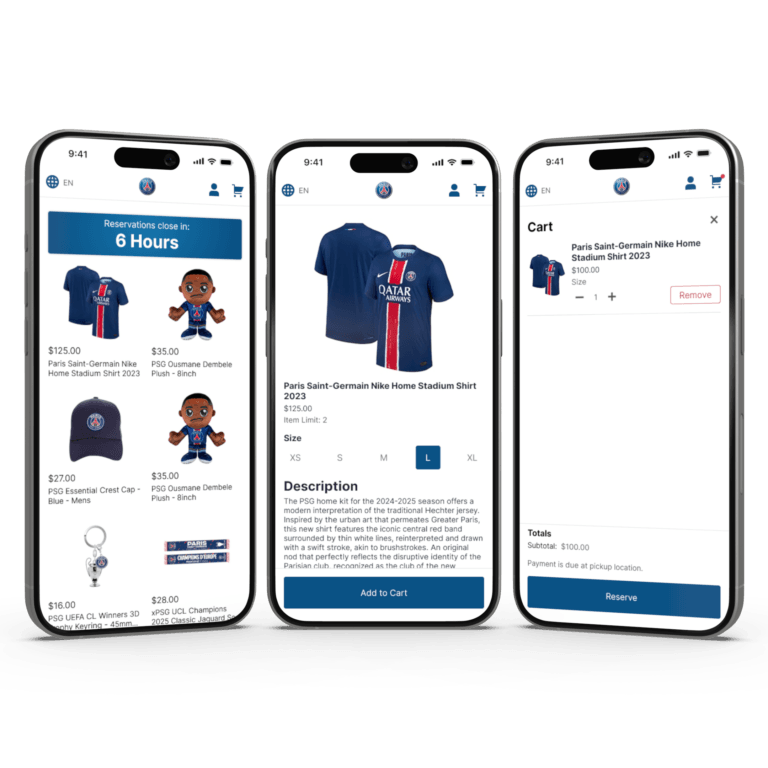
Giving Structure to a Joist Manufacturer
Steel joists give structure to commercial buildings. Each building requires custom, unique joists to meet design needs and building code for their specific location. Weather and other natural disasters dictate how thick the steel must be.
We rebuilt and modernized our steel joist manufacturer client’s complex design and estimation app. Integral to their sales process, the desktop app speeds up key tasks and allows for more accurate raw material estimation.
What We Did
Tech Stack
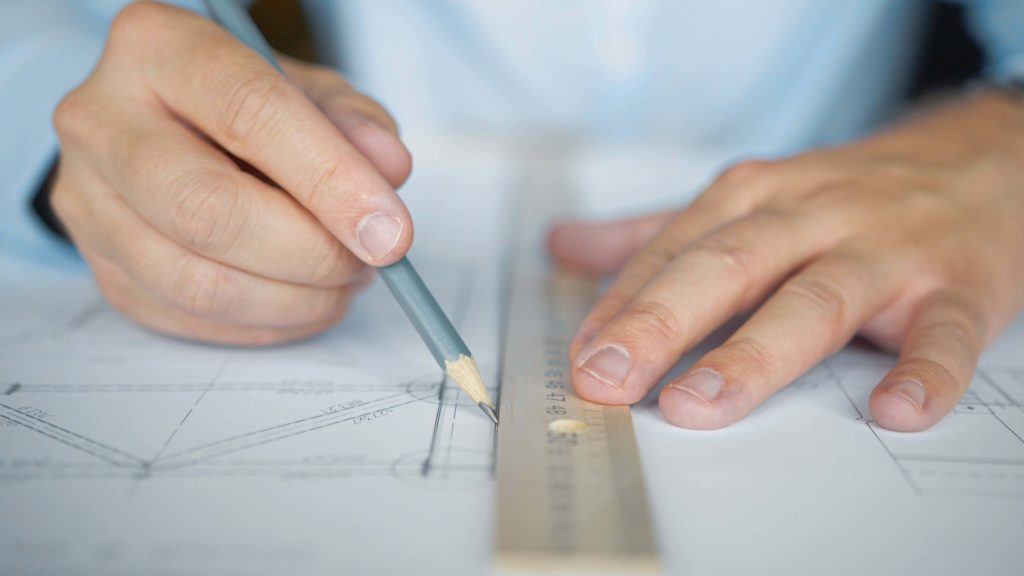
Opportunity
Look up in any commercial building – chances are you’ll notice open web steel joists spanning the ceiling holding everything in place. These joists are integral to the construction of safe, sturdy structures. They transfer the weight of the floor deck or ceiling to the frame of the building. Our client designs and manufactures these joists for their customers. Most buildings require custom joists with a variety of uses, leading to a staggering number of combinations for different sizes, shapes, and materials. Adding to the complexity, it’s highly desirable to minimize the amount of steel used in the joist to reduce costs and environmental impact.
For years, our client used an internally developed software tool to design, estimate, and quote joist projects. As they extended the capabilities of this tool to meet new nuances of their business, it became a critical component of their successful operations. The software served them well, but was becoming difficult to maintain and the underlying technology was becoming unsupported. Our client engaged SEP to recreate the tool.
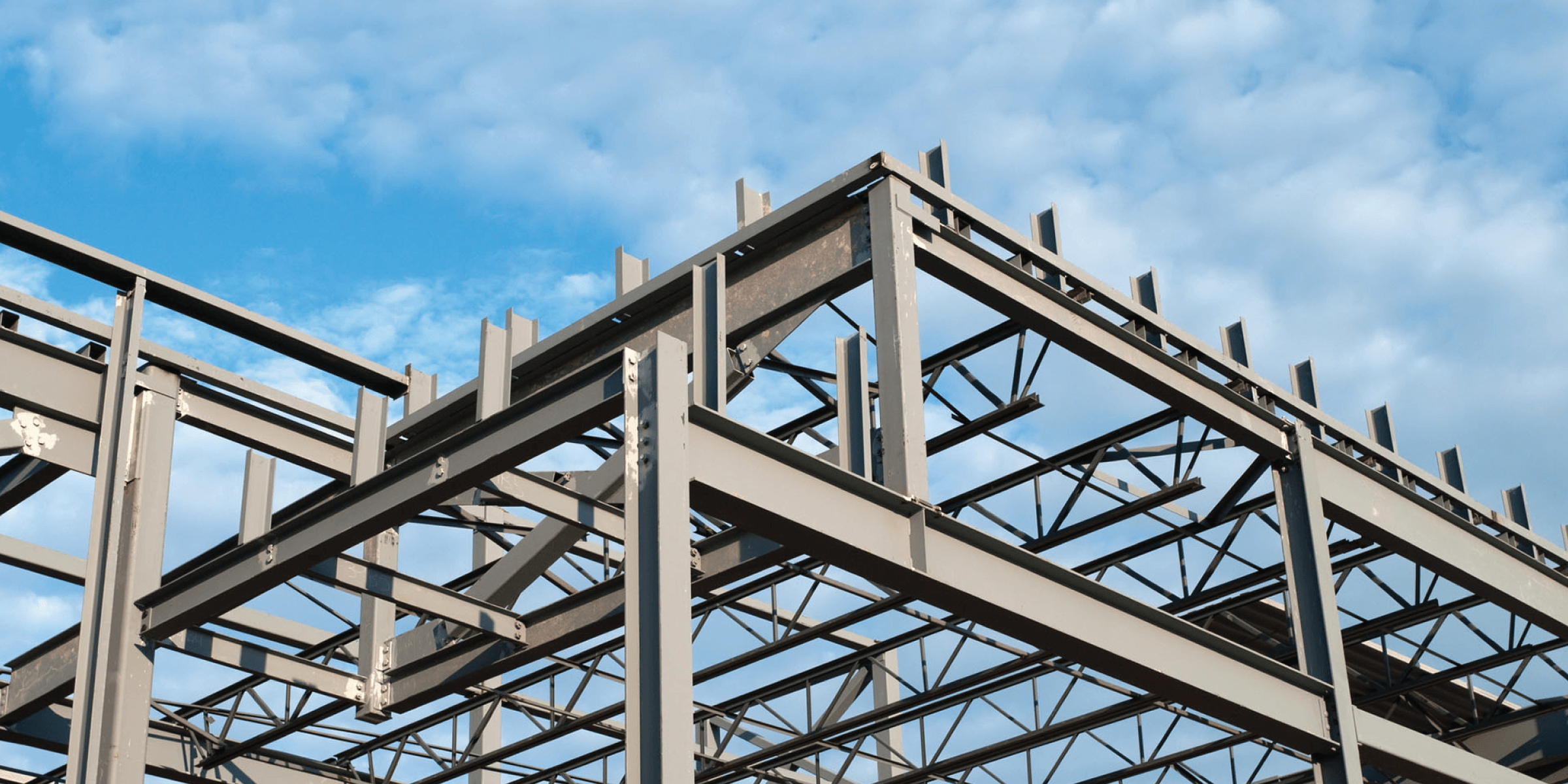
Solution
To begin the process of rebuilding this complex tool from the ground up, we immersed ourselves in the world of steel joists. Our team went onsite engaging with engineers, designers, and sales team members to understand how this software supported their business. We gathered employees from across the United States at our Product Design Studio for collaborative product discovery sessions. We were building a product that they would use every single day to do their jobs – it had to be right. These sessions created shared understanding across roles and locations not just for us, but for our client stakeholders.
Our client has several different manufacturing locations spanning the U.S. that all do the same work in unique ways. Due to this added complexity, we put a heavy focus on interaction design and user research throughout our engagement. We gathered users from each location for design studio sessions. One of SEP’s interaction designers traveled to our clients’ sites to conduct paper and high-fidelity prototyping. These activities allowed us to regularly vet visual and interaction designs with key users.
This line of business application is essential to our clients’ day to day work, so we needed to replace it carefully and incrementally. We started by re-engineering the back-end . We used a hybrid development approach to incrementally transition from the old tool to the new desktop app. This product thinking approach (versus a project-centric one) helped us deliver value faster by leveraging features from both the old tool and the new one simultaneously.
Working alongside our client’s engineers, we operated co-make style to build the desktop app. We used Azure DevOps and video conferencing to coordinate our work with multiple development teams.
We built the client-server architecture using a WPF desktop client and ASP.NET Core services running on Docker containers. This let the software scale the calculation-heavy operations to the server, rather than the user’s computer.
We delivered the app to the client’s sites in phases in accordance with their business and user needs. As part of the deployment, members of our product team traveled to each site to observe the new user experience and train new users. The feedback and questions we received helped us make actionable changes to the app and informed future product design decisions.
Results
We began the engagement with the end goals of driving down steel usage and increasing the efficiency of end-users. To date, we have launched features that save users’ time – frequently used, repetitive actions can now be done in bulk. Certain tasks that used to take hours of work now only take minutes. We’re heading into the most fruitful joist analysis component of the product, which will yield meaningful steel savings.
Recent Case Studies
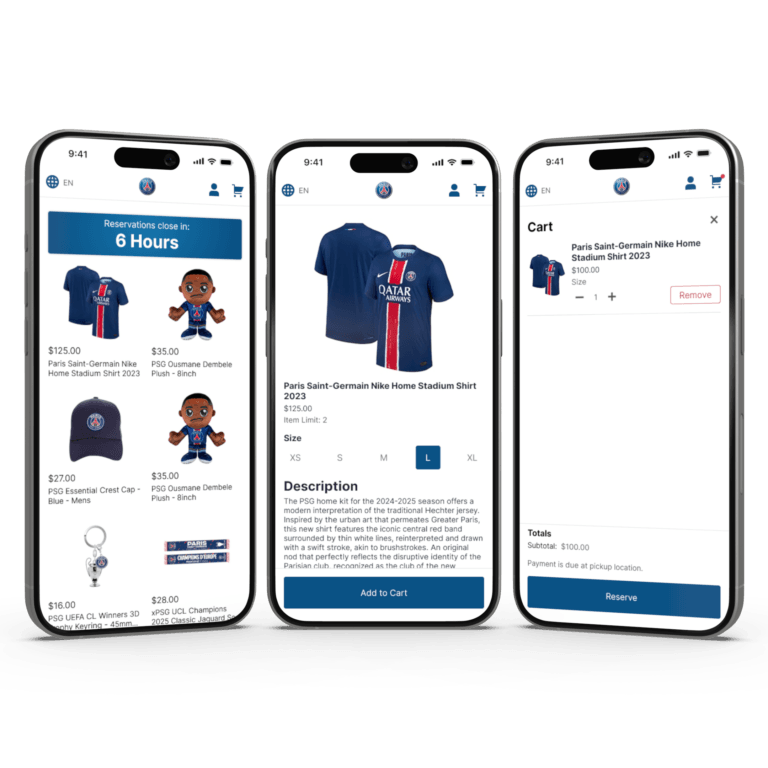
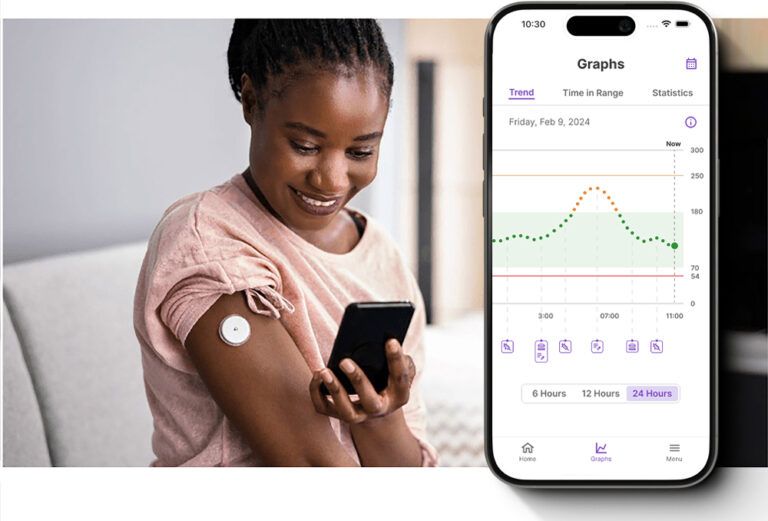
Empowering Patients with a Groundbreaking User-Friendly CGM

Crafting Luxury Smart Home Solutions: The Power of Tech-Enabled Innovation
Let’s develop something special.
Reach out today to talk about how we can work together to shake up your industry.