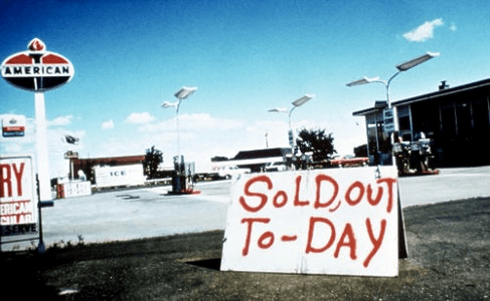
US car companies were booming in the early 1970’s. Americans loved big cars and had cash to buy them. Demand for oil rose so quickly that, by 1969, the US began importing oil. Not long after, oil exporting nations began using US dependence on their oil to influence US foreign policy.
During the first embargo in October, 1973, gasoline prices skyrocketed as oil nations sought to influence US foreign policy in the Middle East. That embargo set off a chain of events that forever changed the Automotive Industry.
The rise of the Japanese car manufacturers
Although imports increased in the 1960’s, Japanese cars weren’t fashionable in America. But, when rising fuel prices created demand for smaller fuel efficient cars, Japanese manufacturers were ready. The small cars they were already building for domestic customers were quickly adapted for the US market.
US factories were models of mass production. Large sales volume created production forecasts which encouraged over-production. That momentum made it harder for them to adapt to the market shift. Cars like the Chevrolet Chevette and Dodge Omni didn’t hit showrooms until the late 70’s.
Why were Japanese manufacturers so ready?
After World War II, the Japanese economy was in ruins. Japanese consumers had little money for luxury items like cars. Raw materials were scarce and expensive. Car companies could not afford fill their showrooms with unsold cars. Toyota created Just-In-Time Manufacturing to manage material and inventory cost by linking the purchase of materials to the purchase of a vehicle. Showroom sales drove material purchases. Raw materials were earmarked for cars that were already sold.
When US demand rose, Toyota didn’t have to overcome extra materials or unsold inventory and could quickly reconfigure their designs and their factories to build cars for America.
What is Just-In-Time Manufacturing
Just-in-Time Manufacturing sources materials to build only what is needed at the precise time it is needed. Sometimes called pull manufacturing, product is pulled through the factory as the next operation has capacity. If a station stops, all prior stations also stop. In-process materials don’t accumulate at earlier production steps. Toyota began using Just-In-Time manufacturing in 1937.
Pull manufacturing created Kanban. Kanbans are a visual system for arranging raw material on the factory floor ahead of the next manufacturing step. When the prior operation fills the kanban, production stops at that station. Kanbans limit the amount of work in progress and minimize waste from rework and overproduction.
Jidoka recognizes that the people building the cars know the most about the process. It obligates production operators to identify problems and offer suggestions. Jidoka created a culture of constant change. Toyota called the concept Kaizen.
Employee driven change created a culture of internal communication. Toyota created Quality Circles, a daily employee-led meeting to review the impact of process improvements, suggest new ones, and plan their incorporation into the standard workflow.
Toyota paired Just-In-Time Manufacturing with Jidoka to create the Toyota Production System.
What does any of this have to do with software?
Many software teams use Kanban boards to track their development process. It visualizes the process of pulling stories through development and helps teams manage work-in-progress
Jidoka and Kaizen created the culture of change at Toyota. Today, we recognize this as “Responding to change over following a plan” from the Agile Manifesto.
Software developers will recognize Quality circles as Stand-up Meetings
How did we get from Toyota Production System to Lean Software Development?
Toyota began printing the Toyota Production System in 1973 and sharing it with their suppliers. Ten years later, they entered a partnership with General Motors to build cars in the US. But, it wasn’t until 1996 that General Motors published their Global Manufacturing System, which copied the Toyota Production system.
In the mid 1970’s, James Womack was studying global manufacturing practices. In 1990, Womack partnered with Daniel Jones to publish The Machine That Changed the World. They coined the term Lean Production and brought lean manufacturing to factories around the world. They later founded the Lean Enterprise Institute, leveraging the principles of the Toyota Production System.
Mary Poppendieck learned Japanese manufacturing techniques while working at a video tape manufacturing plant in the mid 1980’s. She used Just-In-Time to reconfigure the factory and empower operators to improve the processes. As a result, the factory had less inventory, higher quality, lower cost, and faster response to customer changes. Tom Poppendieck was an expert in software product development. Together, they brought Lean Manufacturing to software development with their 2003 book Lean Software Development. Their book introduced the Toyota Production System to the software development world.
Would this have happened anyway?
Yes, probably. Even with the wake-up call of the 1973 embargo, US manufacturers were slow to adopt lean. By the time General Motors fully embraced lean in 1996, Toyota had been perfecting it for 60 years. By 2006, Toyota was the largest automotive manufacturer in the world.
So, maybe slow US adoption served to highlight the value of lean. The weakening of US car manufacturers, set in motion by the embargo, provided the ideal case study. Without the embargo, the benefits of lean may not have been as pronounced in James Womack’s case studies.
Had lean manufacturing techniques been slower to reach the US, Mary Poppendieck’s optimizations for the video tape factory may have taken a different direction. Possibly, a direction much less interesting to the software development process.