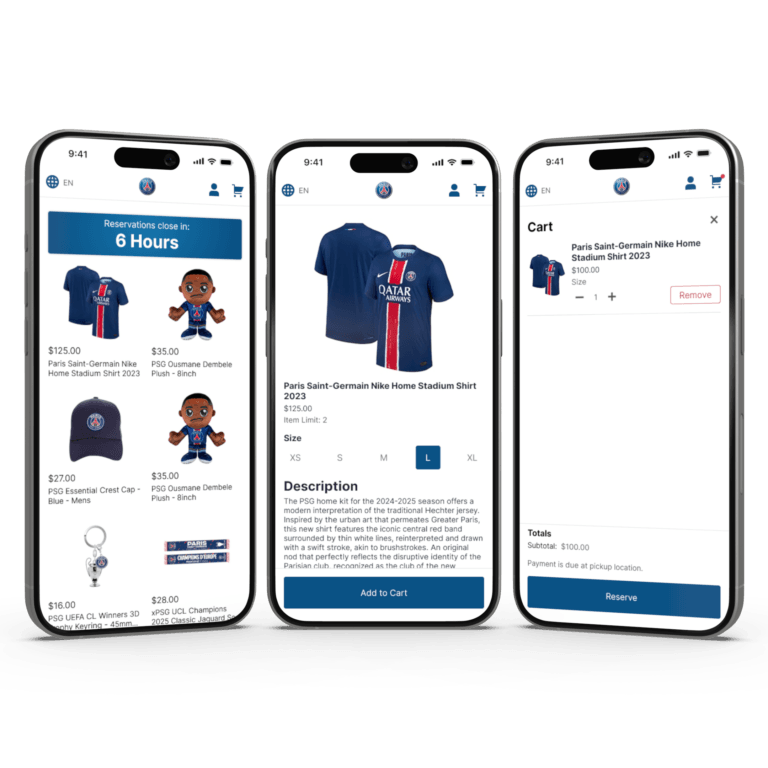
Preventing Rework in the Field
An agricultural equipment manufacturer needed a solution for transmitting telemetry data from one ag machine’s embedded display to other machines’ via a cellular network in near-real time.
We teamed up with our client to bring this new feature to life. Our client’s new product offering became much more attractive to customers with the addition of this key feature.
What We Did
Tech Stack
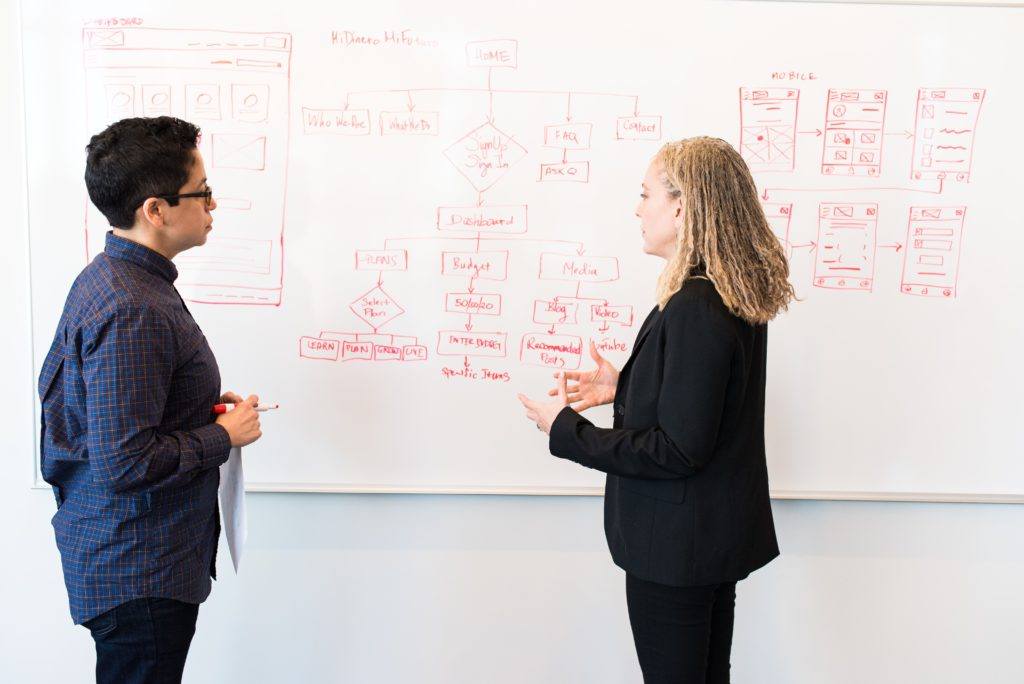
Opportunity
Modern farming relies on an infrastructure of technology to efficiently power machines across acres of farmland. Our client provides that equipment and those technology solutions to support farmers in feeding, clothing, and fueling the world.
Since we had teamed up before, our client knew we could solve any problems they sent our way. They wanted to add in-field communications to the embedded displays inside their tractors and other agricultural machines. By integrating this capability into the existing machine displays, our client could move away from their existing add-on solution. It would also provide farmers everything they need in one purchase rather than buying the main product and the communications add-on. This field work sharing feature would show tractor operators the areas that other operators had already covered, preventing rework and waste of materials.
Our client needed this feature to stay competitive in the market and encourage customers to switch to their new product.
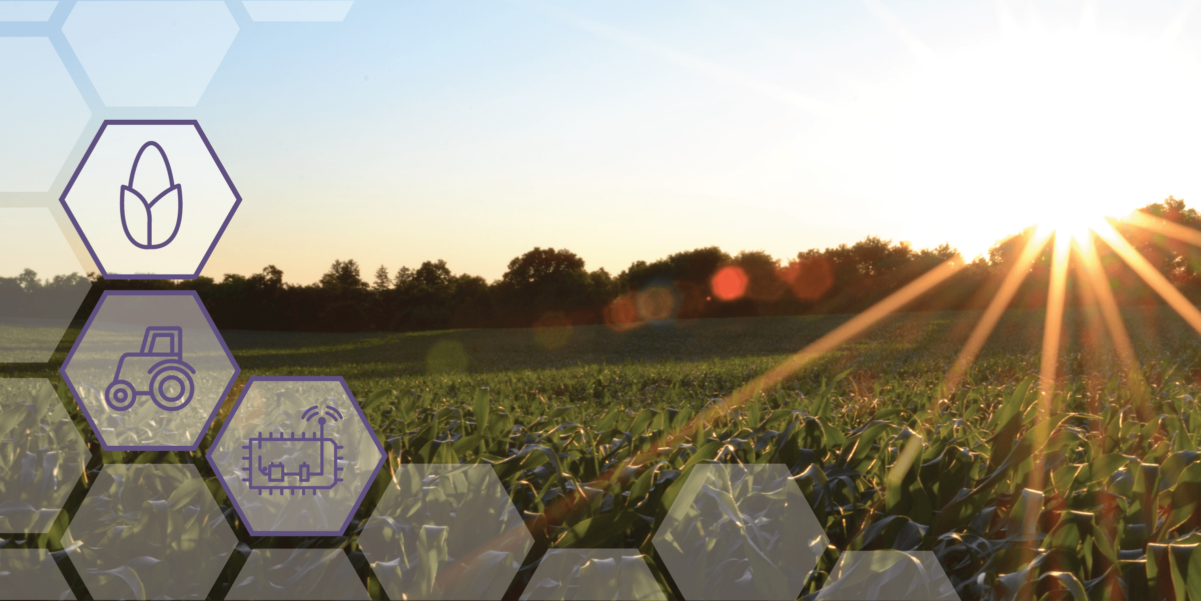
Solution
Our client engaged us to mirror the functionality of the previous add-on solution. We built the new tool on embedded infrastructure our client had built in Linux.
We facilitated a user story mapping session onsite with multiple development teams so everyone had an understanding of the high level goals of the effort. As debugged complex issues along the way, coordination was crucial and required a high level of communication and teamwork across teams.
We wrote code to transmit telemetry data between equipment via a cellular network. Transmission happens in near-real time, allowing all machine operators to reduce overlapping work in a given field. Our efforts also made the data available for statistical analysis, which we implemented on the display.
We added highly desired features including:
- A 2D display of the field that would show a 3D model of where other vehicles are positioned, alongside a customizable machine name.
- The ability to resume previous jobs. Machine operators oftentimes started planting or spraying a field, but would need to stop and pick up the work the next day. Our feature allowed them to resume the job even from a different machine.
We centralized a machine operator’s data into their account, preventing them from having to import and export data manually.
Our work also allowed for improved section control, meaning that the machine would automatically stop planting if an area of the field had already been planted. We built this to work with inch-level accuracy using GPS data.
Results
Our client was thrilled with our ability to complete this project within their desired timeline. The final product not only mirrored the functionality of the old solution, but we were able to build functionality to send full telemetry data which they didn’t think was possible. The new product now helps machine operators and farm managers improve efficiencies and yields on their farms and reduces the likelihood of redundant work in the fields.
Check out the other engagements we went on to do with this agricultural client: Heavy Machinery Monitoring and Agricultural Fleet Optimization.
Recent Case Studies
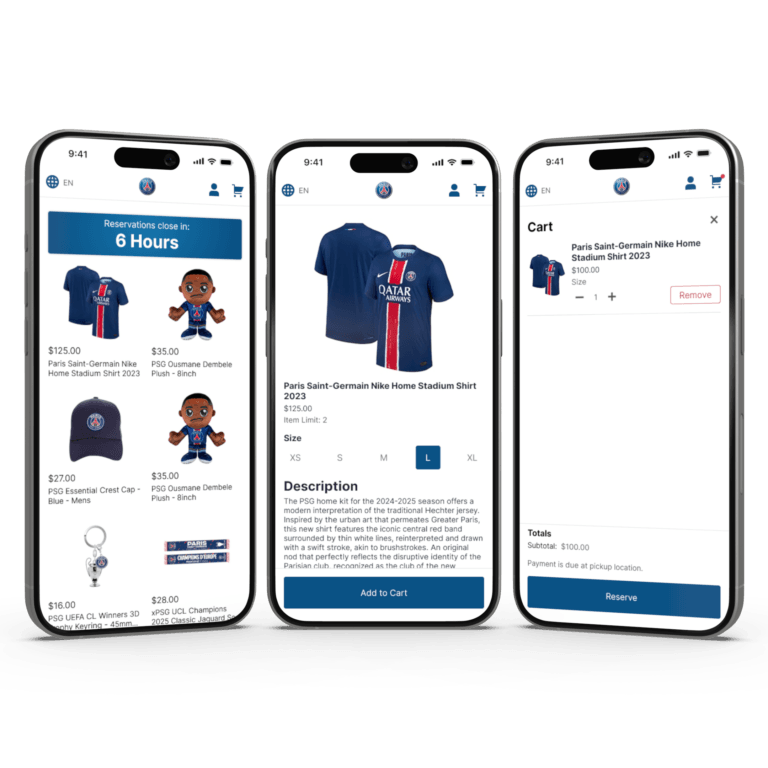
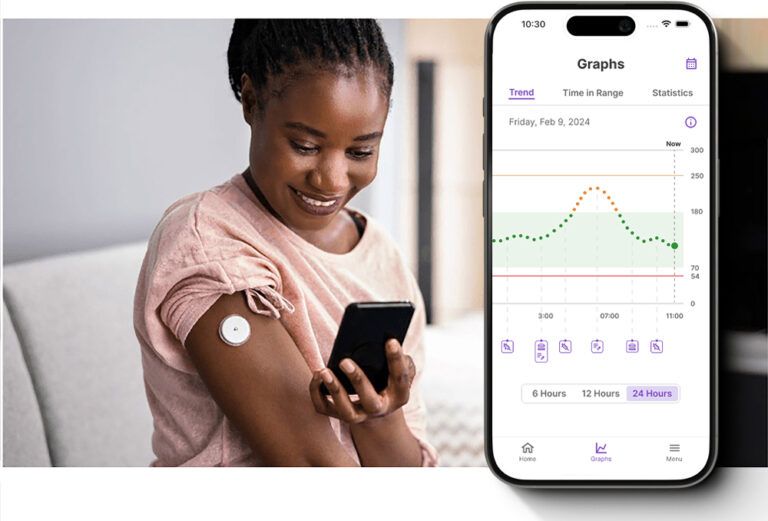
Empowering Patients with a Groundbreaking User-Friendly CGM

Crafting Luxury Smart Home Solutions: The Power of Tech-Enabled Innovation
Let’s develop something special.
Reach out today to talk about how we can work together to shake up your industry.